What is Blister Packaging?
Blister packaging, Blister Packs, or simply blisters, are terms used to describe several types of pre-formed clear plastic cavities typically used for securely packaging small consumer goods. Often these packages will hang on a merchandising wall. The components of a blister pack consist of a cavity, pocket, or bubble made from clear plastic and a backing (often a paperboard card). It is common to integrate a hanging element of various styles into either the plastic or the backing. Read on to see these effects.
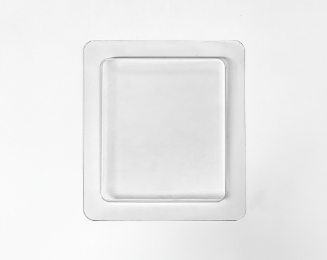
Bubble or Cavity
To design the bubble or cavity, VisiPak customers can send in a sample of the product to be packaged (or a drawing of the design). From either of these, a mold is engineered that will produce a clear, plastic bubble. The type of blister package chosen will affect the cavity design and this includes the type of material, such as PVC or PET plastic.
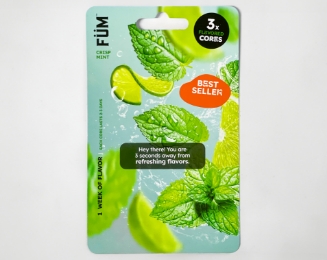
Card or Backboard
While the transparent blister allows one to see the product, most blister packages also include some type of blister card or paperboard. This card (or cards) provides space for graphics and product information which serves to inform and grab the buyer’s attention.
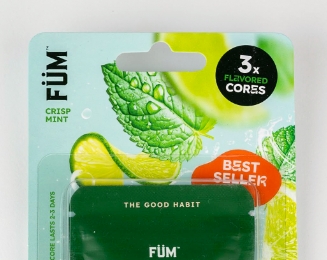
Hanging Element
Given that most blister packs are designed to hang on a merchandising wall, most are designed with some type of hanging feature. Given that paperbaord can rip more easily than plastic, many blister packaging designs feature hang holes that are integrated into the plastic blister. Multiple hanging holes styles are available.
Common Types of Retail Packaging Blisters
There are several different types of blister packaging – Face Seal, Full-Face Seal, Trap, and Slide.
Each one has its unique qualities and price points, from entry level to high end.
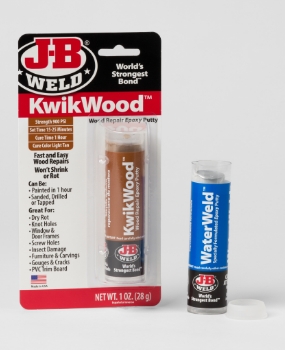
Face Seal Blisters
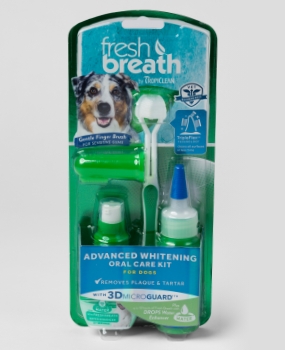
Full Face Seal Blisters
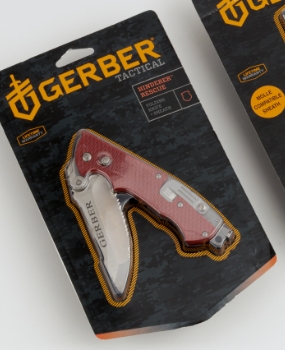
Trapped Blisters
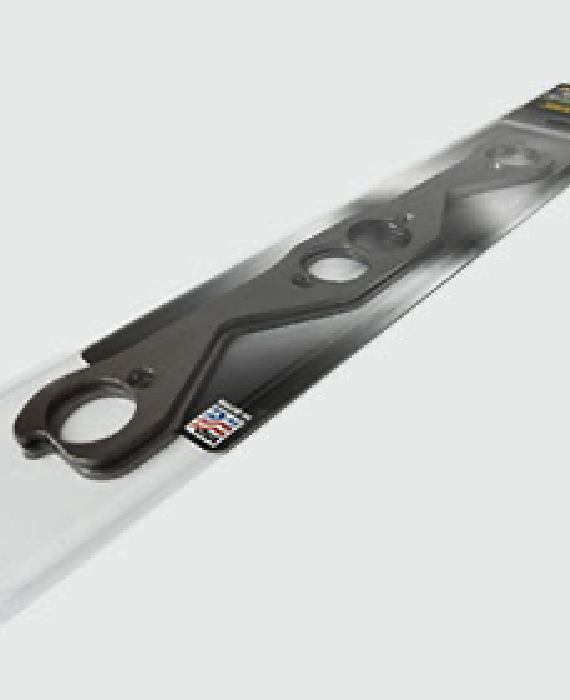
Slide Blisters
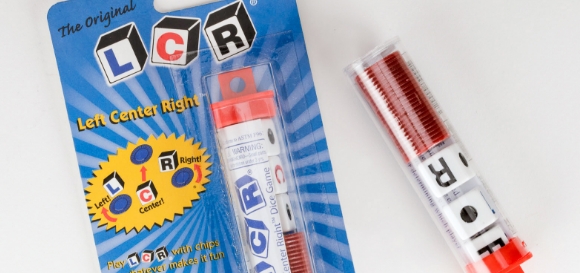
Low Cost
Blister packs typically represent one of the most cost-effective methods for packaging a product. Both the paperboard and plastic blister – which are available in different materials and thicknesses – are inexpensive. Plus, numerous companies make equipment to automate the packing and sealing processes.
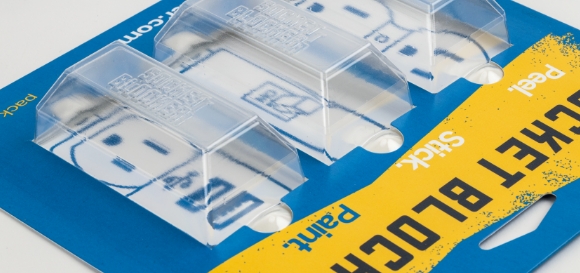
Advertising Space
Given that most blister packs are merchandised on wall displays, they often feature plenty of space for branding and marketing space. Graphics on the cards can be used to help products stand out and may include promotional materials or advertisements to help build brand awareness.
Clear Display of Product
Most consumers believe it is important to see the actual product before making a purchase. Blister packaging allows shoppers to view the product and clearly see a well-protected product, making their purchase decision easier.
Theft Deterrence
Blisters are designed to provide a deterrent to theft by sealing or trapping the product between the blister and the card. Packages are typically designed to be tamper-evident to ward off temptation.
Hanger Options
In addition to offering many different types of blister packs, one can also choose from a variety of hanger options when designing a blister.
Slot Hang Tabs
Hook Hang Tabs
Hole Hang Tabs
Fold Up Hang Tabs
Security Hang Tabs
Applications for Blister Packaging
Blister carded packaging is used in a variety of markets and product categories, including:
- Club Stores
- Major Retail Chains
- Home Improvement, Hardware, Tools
- Hunting and Fishing
- Sports & Recreation
- Health and Beauty, Cosmetics
- Household Goods
- Electronics
- Office and Craft Supplies
- Toys and Games
- Automotive
Pharmaceutical Blister Packs
Another type of blister pack that differs from most retail blister packaging are those designed for pills and tablets. These pharmaceutical blister packs usually consist of a relatively thin blister tray that is lidded with a foil barrier.
These packs allow the medication or supplement to be pushed through the lidding material – providing the tamper evidence obviously critical for these items. This type of sealing is also good for protecting products against external factors like humidity and contamination, and can do so for extended periods of time. Opaque blisters also protect light-sensitive products from UV rays that can negatively affect efficacy.
Blister Trays
The term “blister tray” is another type of blister packaging although we commonly refer to them as thermoformed trays. They are made on the same machines with the same types of plastics, so they are essentially the same as blister packs. The main purpose of a blister is to be sealed to a paperboard card or hung on a merchandising wall.
Still, Blister trays can still be lidded with foil, film or a thermoformed plastic lid. They may function as packaging insert trays. Or, oftentimes, they are used as shipping trays or material handling parts trays.
Steps in Developing a Custom Blister Package
1. Project Begins
- Email, phone call, video meeting or in-person meeting to review:
- Application is discussed.
- Customer supplies example of product or a drawing with dimensions.
- 3D model preferred but not required.
- Goals for packaging and branding are discussed.
- Necessary level of clarity, materials, cleanliness of parts and timeline is established.
- Card Dimensions / Shelf Space available / Planogram is discussed.
- Features or Benefits of product that want to be highlighted are discussed.
- Hang-Hole style determined.
- Customer budget is discussed.
- Estimated pricing and current estimated lead time may be provided
2. Design
- Customer typically is provided with a 2-D design from a VisiPak Packaging Engineer that incorporates what has been discussed.
- Customer reviews design and provides feedback.
- Design is approved or revisions are made and process continues until design approval.
- Final pricing and lead time is provided. Subject to change if changes are made post-approval.
- If a graphics card or trap blister card is needed, we will provide the required die-lines to your art card supplier.
- During this process we will also finalize any packaging requirements for boxes, bags, pallets, etc.
3. Prototyping
- Establish customer credit.
- Customer submits purchase order for prototype.
- Ren board mold is created in-house and blister samples are produced.
- We design and test customer sample for form, fit, and function.
- If only 2D drawing available, instead of actual product, we use software to estimate form, fit and function.
- We ship blister samples to client for approval.
- Customer approves blister or revision is made (1st revision, if minor, typically at no charge).
4. Tool Development
- Client provides written approval of blister and submits purchase order for production of tooling and production parts.
- Initial order for tooling and production parts typically takes between 9 and 13 weeks depending upon the complexity of the part.
- Actual tool design and the first article samples typically takes between 8 and 12 weeks.
- Aluminum mold is manufactured in-house on state of the art CNC equipment.
- Production parts made from the tool, after first article samples are approved, typically takes 1 to 2 additional weeks to produce.
5. Part Production & Fulfillment
- Product is scheduled for production usually within 1 to 2 weeks after First Article approval is provided.
- First production run: We will need to know from you how long your approval process will take. Some customers only need to check the product fit and can give a “same day” approval over a video call. Others need to conduct a drop or ship test. Based on this feedback we either schedule the order to run while the machine is set-up or re-schedule the run based on how long your approval process takes.
- Blisters shipped to customer.
6. Repeat Orders
- Typically plan on a 3 to 4 week lead time to ship repeat orders.
- Our Customer Service Department will be the main contact for processing repeat orders, pricing inquiries and maintaining customer satisfaction.
- Our Sales Department will be responsible for discussing all new opportunities and fielding any technical questions.
- If you have a high volume part(s), we can set up an inventory program for plastic, parts or both, which will cut your lead time down depending on what option you choose.
7. Lead Times
Typical business day lead times after PO and all relevant information has been submitted and acknowledged.
- Concept drawing for new part will be provided in 5 to 7 days.
- Requires email approval from the customer.
- Prototype parts will be available to ship within 7 to 11 days after email approval of concept drawing.
- Modification rounds for prototypes can be 2 to 7 days based on changes requested.
- Requires signed/returned Sample Approval form.
- First articles off production tooling will be available to ship in 8 to 12 weeks after Sample Approval form is received.
- Requires signed/returned First Article Approval form.
- Production will begin 1 to 2 weeks after First Article Approval form is received.
Our Work
Gerber
J-B Weld
TenPoint
SOG
Grease Monkey Wipes
Dr. Brown’s
Lang Pharma Nutrition
Fuji
Strike King
Buck Knives
Socket Blocker
George & Co Games
The VisiPak Difference
Complete Service
From developing the design to specifying the material and providing prototypes, our team can assist you in every step of the packaging development process.
Ready to Get Started?
Request Quote
and/or Samples
Contact sales for volume pricing and
access to free samples for testing and
prototyping.
Contact a
Packaging Specialist
For help finding the best package for
your application or creating one that
is customized to your specific needs.
Shop Our
Online Store
For immediate access to our stock
packaging tubes, clamshells,
containers, caps and more.